Automotive Fuels & Their Properties
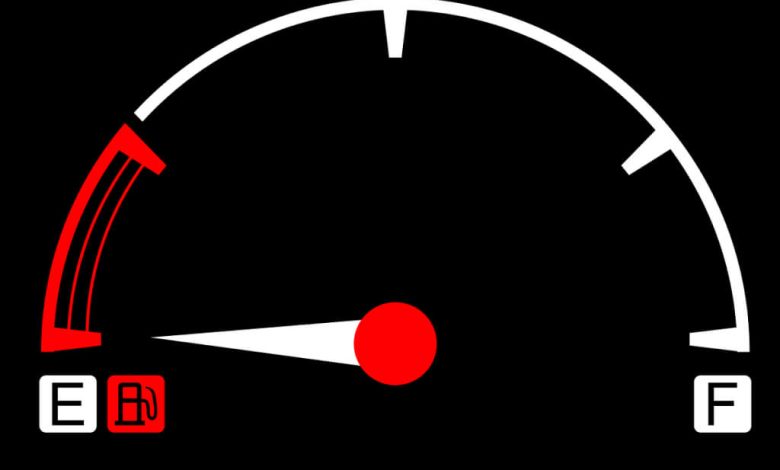
Automotive fuels (Gasoline and diesel) are derivatives of crude oil. Hydrocarbon-based fuels which are gasoline, diesel, natural gas, and liquefied petroleum gas (LPG) have been generally used in the diesel and gasoline engines as a fuel. In this study, hydrocarbon-based fuels such as alkanes (paraffins), naphthenes (cycloparaffins), alkenes (olefins), alkynes (acetylenes), and aromatics (benzene derivatives) have been classified. The approximate elemental structure of an average crude oil consists of 84% carbon, 14% hydrogen, 1–3% sulfur, and less than 1% nitrogen, oxygen atoms, metals, and salts. Crude oil consists of a wide range of hydrocarbon compounds consisting of alkanes, alkenes, naphthenes, and aromatics. These are very small molecular structures such as propane (C3H8) and butane (C4H10) but can also be composed of mixtures of various structures with very large molecules such as heavy oils and asphalt. Therefore, crude oil needs to be distilled to be used in internal combustion engines. As a result of heat distillation of crude oil, petroleum derivatives such as petroleum gases, jet fuel, kerosene, gasoline, diesel, heavy fuels, machine oils, and asphalt are obtained. In general, the distillation of crude oil resulted in an average of 30% gasoline, 20–40% diesel, and 20% of heavy fuel oil, and heavy oils from 10 to 20% are obtained.
During the distillation of crude oil, gasoline is obtained between 40°C and 200°C, and diesel fuel is obtained between 200°C and 425°C. In order to use these fuels in engines, some of the important physical and chemical properties such as specific gravity of the fuel, structural component, thermal value, flash point and combustion temperature, self-ignition temperature, vapor pressure, viscosity of the fuel, surface tension, freezing temperature, and cold flow properties are required. The specific mass, density of the fuel decreases with increasing hydrogen content in the molecule. The density of gasoline and diesel fuels is generally given in kg/m3 at 20°C. The American Petroleum Institute (API) number is an international measurement system that classifies crude oil according to its viscosity according to the American standards. The specific gravity can be defined as the ratio of the weight of a given volume of a given substance at 15.15°C (60°F) to the weight of the water at the same volume and temperature.
While the density of gasoline is ρ = 700–800 kg/m3, it varies between ρ = 830–950 kg/m3 for diesel fuel. While the carbon content in alkane and naphthene fuels is 86%, it is around 89% for aromatics. In addition to carbon and hydrogen atoms, sulfur, asphalt, and water can be found in gasoline and diesel fuels. In particular, sulfur can cause corrosion in engine parts, and the combustion products of sulfur have a negative impact on the environment. The asphalt adheres to the valve on the piston surfaces and causes wear. The water causes corrosion and reduces the thermal value of the fuel. These are undesirable components in the fuel. The thermal values of liquid fuels are given as unit mass energy (kJ/kg or kcal/kg), while the thermal values of gas fuels are given as unit energy (kJ/l, kJ/m3 or kcal/m3). Thermal values of fuels are expressed in two ways as lower and higher heating value. If the water in the fuel is in the vapor state at the end of the measurement, it gives the lower thermal value of this fuel. When the water in the fuel condenses at the end of the measurement, it gives the evaporation heat to the system, and the measured value gives the higher heating value of the fuel. As a result, the single-phase steam is obtained in the calorimeter capsule as a result of the thermal value measurement so that the lower heating value is measured. The dual phase (liquid-vapor phase) is obtained so that the higher heating value is measured. When the temperature of an air-fuel mixture is sufficiently heated, the fuel starts to ignite by itself without external ignition. This temperature is referred to as the self-ignition temperature (SIT) of the fuel and the delay time for the combustion of the fuel to be the ignition delay (ID). The terms SIT and ID are important features of engine fuels. SIT and ID values vary depending on variables such as temperature, pressure, density, turbulence, rotation, air-fuel ratio, and presence of inert gases. Self-ignition is the basic rule of the combustion process in diesel engines. SIT value is desired to be high in gasoline engines and low in diesel engines. The auto ignition temperature of the gasoline is 550°C and higher temperatures.
Depending on the type of gasoline or diesel engine, the desired properties of fuels vary. The most important properties of gasoline fuels are properties such as volatility and knocking resistance, whereas diesel fuels are required to have important fuel properties such as viscosity, surface tension, and ignition tendency. In gasoline fuels, volatility and knock resistance are one of the most important parameters affecting engine performance. The volatility of gasoline fuel affects the rate and amount of evaporation of the fuel in the intake channel and in the cylinder. The low volatility of the fuel influences the formation of sufficient air-fuel mixture, but when it is very volatile, it can prevent the flow of fuel by creating vapor bubbles in the suction channel with the local temperature increases. When the flame front advances during combustion, with the increasing temperature and pressure inside the cylinder, it compresses the air-fuel fill which the flame front cannot yet reach. Thus, the fuel can constitute another combustion front due to the fuel spontaneously reaches the ignition temperature to heat and radiation. The combustion speeds of the flame fronts at these different points can be 300–350 m/s, and cylinder pressures may reciprocate to as high as 9–12 MPa. At these high speed and pressure values, the flame fronts are damped by hitting each other or against the walls of the combustion chamber. These damping are not only cause loss of energy but also increase the local heat conduction. As a result of this situation, engine performance decreases. This phenomenon is called a knock in gasoline engines and is an undesirable situation. The chemical structure of the fuel has a considerable effect on the auto-ignition temperature. Octane number (ON) is defined as the property of fuel to knocking resistance or how well the fuel itself ignites. The octane number is inversely proportional to the chain length of the fuel molecules. The shorter the molecular chain length of the fuels has, the higher the octane number is. However, the octane number is directly proportional to the branched side chain component. The higher the branching in the molecule chain leads to the higher octane number of the fuel. In other words, it causes higher knocking resistance of fuels. Generally, increasing the number of carbon atoms in the composition of the fuel has higher impact resistance. However, the octane numbers of cyclic molecules, naphthenes, alcohols, and aromatics are high. In order to scale the octane number of gasoline, two reference points are taken, which represent points 0–100. The octane number of normal heptane (C7H16) is assumed to be 0, while the octane number of isooctane (C8H18) is considered to be 100. The reason of these two fuels as a reference point is that both fuel compounds have almost the same volatility and boiling point values. The reason as a reference point of these two fuels is that both fuel compounds have almost the same volatility and boiling point values. Fuels such as alcohols and benzenes with an octane number higher than the top octane number of this measure are also available. In gasoline engines, additives are used to increase the knocking resistance of the fuel to prevent knocking. The two most commonly used methods for determining the octane number of fuels are engine method and research method. The octane numbers determined by these methods give the values of motor octane number (MON) and research octane number (RON), respectively.
Since the inlet air temperature of the MON method is higher than the RON method, the post-combustion temperature reaches higher values. Thus, the fuel spontaneously ignites and knocks. Therefore, the octane number obtained by the MON method is lower than the octane number obtained by the RON method because it is operated at lower compression ratios in the MON method. The value difference between these two octane number determination methods is called fuel sensitivity (FS). When the number of fuel sensitivities is between 0 and 10, it is stated that the knock characteristic of the fuel does not depend on engine geometry, and if it is higher than these values, the knock characteristic of the fuel is highly dependent on the combustion chamber geometry of the engine. FS=RON−MONE3
Combustion chamber geometry, turbulence, temperature, and inert gases are the parameters that affect the octane number. The octane number is highly dependent on the flame velocity in an air-fuel charge. As the flame velocity increases, the air-fuel mixture above the spontaneous ignition temperature immediately burns during the ignition delay. Thus, there is a direct correlation between the flame speed and the octane number, as the flame speed will allow the fuel to run out without knocking. Alcohols have high flame speeds, so their octane numbers are high. The ID period does not depend on the physical properties of the fuel such as density and viscosity in a hot engine at steady state. It is strongly dependent on the components of the fuel chemistry. Therefore, additives such as alcohols or organic manganese compounds are added to increase the octane number of the fuel. It is possible to work at higher compression ratios by increasing the octane number of fuels. Thus, high compression ratio increases engine power and provides fuel economy.
Diesel fuels are divided into two main categories as light diesel and heavy diesel fuels. The chemical formula of light diesel is approximately C12.3H22.2, while heavy diesel is considered as C14.06H24.8. The molar weights of light and heavy diesels are approximately 170 and 200 g/mol, respectively. Viscosity, surface tension, and ignition tendency of fuel are important fuel property parameters in diesel fuels. Light diesel fuel has a lower viscosity and requires less pumping work. Since low viscosity also reduces the surface tension of the fuel, the fuel has a smaller droplet diameter during spraying. In contrast to gasoline engines, it is desirable to have a high ignition tendency in diesel engines, since combustion in the diesel engines is based on the spontaneous combustion of the air-fuel mixture. At this point, the cetane number, which is a measure of the fuel’s ignition ability, emerges as a fuel feature. In other words, it is a quantity that quantifies the ignition delay period. Hexadecane (C16H34), a straight-chain fuel of the alkane group, is considered to be the highest reference point of the cetane number, which is the measure of the ignition tendency. The other reference point is cetane number 15 as heptamethylnonane (HMN) C12H34, or the lowest reference point was accepted zero as the cetane number value of alpha-methyl naphthalene C11H10 fuel. First of all, fuel with unknown cetane value is run in the adjustable compression ratio engine. Then, the engine test is carried out until the compression rate at which the first knock starts for determining compression ratio of the fuel. Then, the mixture of these two reference fuels in various ratios is tested at the specified compression ratio, and the reference fuels are mixed until the knocking begins. The percentage of hexadecane at the moment of the knock, in the heptamethylnonane or alpha-methyl naphthalene fuel mixture, gives us the cetane number of the measured fuel. Several empirical equations have been developed by using the physical properties of the fuel since the engine tests are very laborious and costly in determining the cetane number. These methods, which measure the fuel propensity to ignite, are called cetane index, aniline point, or diesel index. Aniline is an aromatic compound which is very easily mixed with compounds of its group even at low temperatures, while it is more difficult to form mixtures with alkanes (paraffins). Therefore, hexadecane (C16H34) which is an alkane group and has a high ignition tendency has a high mixing temperature with the aniline. The mixture of the sample fuel with the same amount of aniline is heated to find the diesel index. Then, all of the aniline is dissolved in the fuel. After that the mixture is cooled for allowing to aniline to separate from the fuel. This temperature, where the aniline is separated from the fuel, is called the aniline point. The diesel index is calculated with the aniline point and API grade specifications.
Diesel index=Aniline point°F×APIat60°F100E4
The higher the diesel index value, the fuel is more alkane (in paraffinic structure), and it has the higher ignition tendency. Increasing volatility in diesel fuels causes acceleration of fuel evaporation and decrease in viscosity. This is generally undesirable since the fuel causes a reduction in the cetane number.
Some fuels commonly used in engines are presented in following table.
Some of the important properties of fuels such as the closed formulas, molar weight, lower heating value and higher heating value, stoichiometric air/fuel and fuel/air ratios, evaporation temperature, motor octane number (MON), research octane number (RON), and cetane number are given.
The cetane index can be calculated from following Equation. which is shown by distilling the fuel. It is calculated from the temperatures and the density of the vaporized fuel at 10, 50, and 90% volumetric ratios by the distillation of the fuel:
SI=45.2+0.0892T10−215+0.131T50−260+0.523T90−310+0.901BT50−260−0.420BT90−310+0.00049T10−2152−0.00049T90−3102+107B+60B2E5
The values of T10, T50, and T90 are the temperatures at which the fuel evaporates in volume ratios of 10, 50, and 90%, respectively. B = −exp[−3500(ρ− 850)] − 1, where ρ = density in kg/m3 at 15°C. This formula is related to the number of cetane, unless cetane-enhancing additives are added to the fuel. Otherwise, the cetane number of doped fuels can be measured by engine test experiments. Another method used to calculate the cetane index is the empirical equation given in following Equation. which is calculated using some physical properties of the fuel.
SI=−420.34+0.016G2+0.192Glog10Tgn+65.01log10Tgn2−0.0001809Tgn2E6
where G = (141.5/Sg) −131.5 is the API degree of the fuel. Sg and Tgn are the relative boiling point temperature in °F and relative density, respectively.
The semi empirical expression that predicts ID duration based on cetane number and other operating parameters is as follows:
ID=0.36+0.22UpexpEA1/RuTemεk−1−1/17.19021.2/Pemεk−12.40.63E7
ID (°CA) is a time in crankshaft angle, EA = (618.840)/(cetane number + 25) activation energy, Ru = 8.314 kJ/kmol K universal gas constant, Tem and Pem temperature at the beginning of compression time, respectively, (K) and pressure (bar), ε = compression ratio, and k = cp/cv = 1.4 are the values used in air standard cycle analysis. ID is calculated by the formula given in following equation. It is expressed in milliseconds for an engine at n rpm.
IDms=DºCA/0.006nE8
The low cetane number of diesel engines leads to an increase in ID time, which in turn reduces the time required for combustion and CA. An increased TG time leads to accumulate more fuel in the combustion chamber than required. Thus, this excess fuel causes sudden and high-pressure increases during the onset of combustion. These sudden pressures increase cause mechanical stresses and hard engine operation, which is known as diesel knocking.
In brief, the number of cetane and the number of octane refer to the spontaneous combustion of fuels. A higher cetane number indicates that diesel fuel burns suddenly and easily. The high octane number defines the resistance of gasoline to sudden ignition. Generally, if the cetane number is high, the octane number is low. There is an inverse relationship between these two properties, so that the cetane number is low if the octane number is high.
Natural gas and liquefied petroleum gas (LPG)
Natural gas is a gas mixture containing methane, ethane, propane, pentane, and hexane in a lighter content than air, without color, smell, and taste. However, it contains a small amount (0–0.5% by volume) of carbon dioxide, nitrogen, helium, and hydrogen sulfide gas. Generally, this gas composition contains about 70–90% of methane, 0–20% ethane, and slightly less propane than ethane. The natural gas used in the market is refined and separated from other gases and used as almost pure methane gas (CH4). Natural gas can be stored as compressed natural gas (CNG) at high pressures such as 16–25 MPa or liquid natural gas at low pressures such as 70–210 kPa and at very low temperatures such as −160°C. Natural gas can be stored by these methods and generally used as compressed natural gas (CNG) in internal combustion engines with a single-point spray system. The single-point spraying system allows for the most efficient use of natural gas as it provides a longer mixing time than required for natural gas.
Table shows the compounds that form natural gas and boiling points.
There are dual fuel diesel engines in which natural gas and diesel fuels work together. Natural gas is supplied to the combustion chamber at approximately sound speed. This leads to high turbulence and high flame speeds. Natural gas has lower combustion temperatures than diesel fuel, and with late spraying, the combustion chamber temperature can be further reduced. Decrease in combustion chamber temperature significantly reduces NOx formation. However, the low carbon content in natural gas leads to less CO2 emissions and much less solid particulate matter.
Dump gas engines, converting methane gas into energy, are one of the most common natural gas applications. Gases produced in landfills generally contain between 45 and 65% methane. In addition to methane, these landfill gases contain highly polluting and variable quality gases such as fluorine, chlorine, silicon, and solid particles. Especially due to the corrosive and abrasive effect of these gases, special piston and valve materials must be used in the engines. The thermal value of natural gas is between 33.4 and 40.9 MJ/m3. CO2, H2O, and 891 kJ of energy are obtained when 1 mol of methane gas is fully combusted. The combustion equation of 1 mol of methane is as described in following equation.
CH4g+2O2g→CO2g+2H2Ol+891kJE9
The high flame velocity and octane number 120 of the natural gas enable the natural gas to operate at high compression rates. This ensures that natural gas is a good gasoline engine fuel. Furthermore, natural gas has low exhaust emissions. In addition, the most important advantage of natural gas fuel is that natural gas can be produced from a source such as coal that has a lot of reserves all over the world. However, since the low-energy capacity of natural gas is in the form of gas, its low volumetric efficiency leads to reductions in engine performance. The disadvantages of this fuel are that natural gas requires high-pressure fuel storage tanks; refueling takes time and has variable fuel components in the content of natural gas. Table presents the properties of natural gas and its comparison with other fuels as thermal values.
LPG, a liquefied petroleum gas, is produced as a by-product from natural gas production processes or during the distillation of oil in refineries. In general, it contains 90% propane, 2.5% butane, and a small amount of ethane and propylene with heavy hydrocarbons. These propane and butane gas ratios in LPG may vary according to the regions and areas of use. In recent years, propane-butane mixtures in different ratios (80% propane/20% butane, 70% propane/30% butane, 50% propane/50% butane) have been tested as fuel in vehicles. LPG gas used in Turkey consisted of 30% propane and 70% butane. LPG is the most preferred fuel type after gasoline and diesel fuels, since LPG is much easier to store and transport than natural gas.
LPG is a colorless, odorless, nontoxic, and easily flammable gas. LPG is a mixture of propane and butane gas, which is gas at normal pressures and temperatures. However, LPG is a liquid at moderate pressure. Besides, it is two times heavier than air and half weight of water. Therefore, LPG leaks to the floor in case of leakage. LPG in liquid state expands to approximately 273 times its liquid volume. This is called sudden expansion and cooling of the sudden temperature drop with the very rapid evaporation of the liquid fuel as it passes into the gaseous state. Since this can cause cold burns, the gas should not be touched with bare hands. Although LPG is a noncorrosive gas, it can melt paint and oil and also inflate natural rubber materials, causing them to lose their properties. Therefore, the use of LPG compatible materials in autogas systems using LPG is very important for safety. LPG system is widely used in gasoline vehicles. With respect to this, the comparison of physical and chemical properties of propane and butane gases which are components of LPG and the gasoline fuel is given in Table.
Gasoline additives:
Gasoline Additives increase gasoline’s octane rating or act as corrosion inhibitors or lubricants, thus allowing the use of higher compression ratios for greater efficiency and power. Types of additives include metal deactivators, corrosion inhibitors, oxygenates and antioxidants.
Some additives are harmful and are regulated or banned in some countries.
- Oxygenates
- Alcohols:
- Methanol (MeOH)
- Ethanol (EtOH); see also Common ethanol fuel mixtures
- Isopropyl alcohol (IPA)
- n-butanol (BuOH)
- Gasoline grade t-butanol (GTBA)
- Ethers:
- Methyl tert-butyl ether (MTBE), now outlawed in many states of the U.S. for road use, mostly because of water contamination.
- Tertiary amyl methyl ether (TAME)
- Tertiary hexyl methyl ether (THEME)
- Ethyl tertiary butyl ether (ETBE)
- Tertiary amyl ethyl ether (TAEE)
- Diisopropyl ether (DIPE)
- Alcohols:
- Antioxidants, stabilizers
- Detergents; see also Top Tier Detergent Gasoline
- Amines aka “nitrogen enriched”
- Polybuteneamine (PBA)
- Polyetheramine (PEA); see also Techron
- Polyisobutyleneamine (PIBA)
- Amines aka “nitrogen enriched”
- Antiknock agents
- Tetraethyllead (TEL), now banned almost everywhere for causing brain damage.
- Methylcyclopentadienyl manganese tricarbonyl (MMT) is an extremely poisonous neurotoxic substance and is fatal if swallowed/inhaled and will cause a disease similar to Parkinson’s called manganism.[1]
- Ferrocene highly toxic[2]
- Dimethyl methylphosphonate
- Toluene
- Isooctane
- Triptane
- Lead scavengers (for leaded gasoline)
- Tricresyl phosphate (TCP) (also an AW additive and EP additive)
- 1,2-Dibromoethane
- 1,2-Dichloroethane
- Fuel dyes, most common:
- Fuel additives in general
- Ether and other flammable hydrocarbons have been used extensively as starting fluid for many difficult-to-start engines, especially diesel engines
- Nitromethane, or “nitro”, is a high-performance racing fuel
- Acetone is a vaporization additive, mainly used with methanol racing fuel to improve vaporisation at start up
- Butyl rubber (as polyisobutylene succinimide, detergent to prevent fouling of diesel fuel injectors)
- Ferrous picrate is used in Diesel fuel to increase fuel conversion efficiency and reduce emissions.
Racing formulations
- Nitromethane can increase the cetane number of diesel fuel, improving its combustion properties
- Nitrous oxide, or simply nitrous, is an oxidizer used in many forms of motorsports such as drag racing and street racing.
Fuel additives in the United States are regulated under section 211 of the Clean Air Act (as amended in January 1995). The Environmental Protection Agency (EPA) requires the registration of all fuel additives which are commercially distributed for use in highway motor vehicles in the United States,[3] and may require testing and ban harmful additives. The EPA also regularly reviews the health and net economic benefits of Clean Air Act policies.[4]
The act also requires deposit control additives (DCAs) be added to all petrol. This type of additive is a detergent additive that acts as a cleansing agent in small passages in the carburetor or fuel injectors. This in turn serves to ensure a consistent air and fuel mixture that will contribute to better gas mileage.
Diesel fuel additives:
Until the latter part of the twentieth century there was little or no use of diesel fuel additives. Due the versatility and robustness of the diesel engine, suitable diesel fuel could be produced from a blend of straight-run atmospheric distillation components. Where a refiner had a necessity to bias production towards gasoline then the diesel pool could often be supplemented with cracked gas oils from the gasoline refining process. As fuel sulfur levels were gradually reduced then additional processing could be required depending on the crude oil source. With the increasing fuel demand, changing demand mix and tightening specifications the refining processes have changed and with it the use of diesel fuel additives. Although there is no rigorous definition of what constitutes an additive, as opposed to a blending component, it is generally accepted that an additive is something added at less than 1% w/w (i.e. 10,000 mg/kg or 10,000 ppm). Because of this low treat rate of additives the physical properties of the fuel, such as density, viscosity, and volatility are not changed significantly.
To increase the yield of diesel fuel the refiner must cut deeper into the crude feedstock; necessitating the use of flow improvers to restore the low temperature performance of the fuel. With increasing demand for improved ignition quality and increasing cetane number specifications the use of ignition improver additives has also risen. As legislation specifying ultra-lower fuel sulfur levels has spread, the ability of the diesel fuel to lubricate the fuel injection equipment has diminished; this has necessitated the use of lubricity additives. The additives discussed in this section can be categorized as follows:
- Fuel handling and distribution additives
- Low temperature operability additives
- Flow improvers
- Wax anti-settling additives
- Cloud point depressants
- De-icing additives
- Other fuel handling additives
- Antifoam additives
- Drag reducing additives
- Static dissipater additives
- Biocides
- Demulsifiers
- Dehazers
- Corrosion inhibitors for fuel distributiuon system
- Marker dyes
- Deodorants and re-odorants
- Low temperature operability additives
- Fuel stability additives
- Antioxidants
- Stabilizers
- Metal deactivators
- Dispersants
- Engine protection additives
- Corrosion inhibitors for vehicle fuel system
- Injector cleanliness additives
- Lubricity additives
- Combustion additives
- Ignition improvers
- Smoke suppressants
- Combustion catalysts
The more widespread inclusion of biodiesel as part of the diesel fuel blend will also necessitate the use of fuel additives. However, these additives will usually be included in the biodiesel itself in order to ensure that the biodiesel meets the relevant specification. This is discussed in greater detail under Biodiesel—Mono Alkyl Esters. Therefore, blending diesel fuel with on-specification biodiesel should not require additional additization.
Conclusions:
Natural crude oil or fossil-based fuels such as diesel, gasoline, natural gas, and LPG have been commonly used in engines as a fuel. Different types of engine uses different fuels defending thermodynamic cycles, Therefore, fuels can be demonstrated in different properties with each other. For example, gasoline fuels should have a high ignition resistance, while diesel fuels should have well self-ignition. For these reasons, hydrocarbon fuels can be converted by some chemical process depending on the engine types or by improving fuel properties. Thus, new fuel formulas or various fuel properties can be improved by converting hydrocarbons each other via some of the chemicals process.
Diesel and gasoline engine fuel properties such as cetane number, octane number, viscosity, and density can be improved by fuel additives. One of the most promising fuel additives are alternative fuels in the future. High octane number and low density propensities of the alcohols lead to be improved the fuel properties such as increases the octane number of gasoline and decreased the viscosity, density properties of the diesel fuel. Besides, the diesel fuel cetane number can be improved by biodiesel, which has a high cetane number.
Sources:
https://www.intechopen.com/chapters/69204#tab3